BHP is a world-leading resources company, working in more than 90 locations worldwide and their products are sold globally.
They’ve positioned business to support the megatrends shaping our world. Iron ore and metallurgical coal for the steel needed for global infrastructure and the energy transition. Copper for renewable energy. Nickel for electric vehicles. BHP is moving into potash to support more sustainable farming.
Let’s see how BHP, a major mining company, uses drone technology to address these challenges and improve its operations.
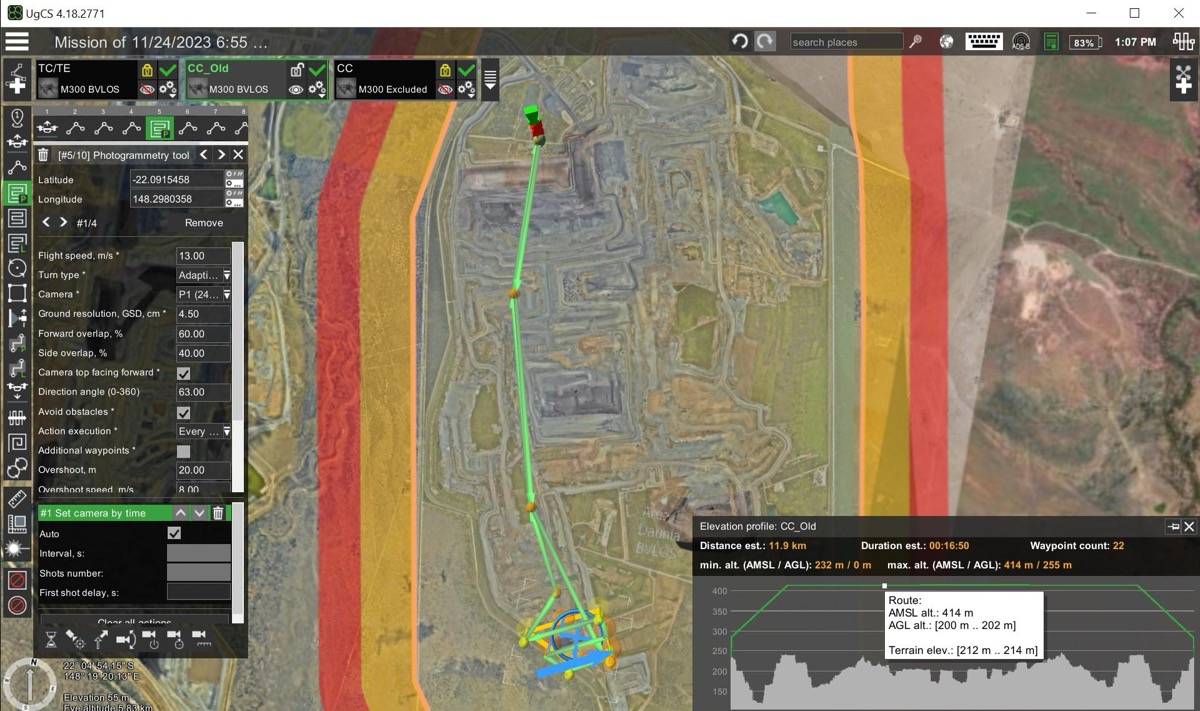
Two key processes
- Obtaining mining surface information:
Mining surface information is captured daily by multiple pilots and drones at each mine site, focusing on areas up to 40km long but typically operating within 1.5km from the takeoff point. With a range of government approvals, surveys cover up to 10 km^2 in a single flight. Flights usually require one battery, though larger surveys necessitate hot-swapping 2-3 batteries. During simultaneous operations, drones navigate at different altitudes or use time separation for deconfliction. Nadir jobs are processed in under 30 minutes, whereas high wall surveys take slightly longer due to their complexity. All surveys are captured with the DJI P1 camera. Without 4G/5G connectivity, data is saved on an SD card and physically transported back for processing, which takes 15-30 minutes. The processed data, imported into a live 3D mine program, enables the extraction of critical safety information and assists production teams in planning. Flight plans utilize photogrammetry or corridor survey models, incorporating custom GEOTIFF elevation models and TIFF background images loaded onto tablets nightly. Planning accounts for large machinery and rapidly changing terrain with near-vertical walls. Pilots choose optimal locations for visibility and safety, mindful of hazards like large haul trucks. Data processing uses an in-house photogrammetry solution that leverages machine learning, marking a significant improvement in speed, cost-effectiveness, and safety compared to the previous method of terrestrial laser scanning, which was more expensive, time-consuming, and often resulted in incomplete data. - Measuring stockpile volumes:
Stockpile volumes are measured weekly, focusing on areas approximately 1.2km by 1km. These surveys are typically covered in a single flight, using just one battery. To manage airspace during parallel jobs, pilots employ vertical separation. Results are delivered from flight planning to report generation within an hour. The surveys use photo sensors, and in the absence of 4G/5G connectivity, SD cards with collected data are driven back to the office for processing. This process is crucial for accurate coal planning for blending. Flight plans are created using corridor and photogrammetry missions, incorporating custom elevation models generated and uploaded daily to ensure precision. Special consideration is given to flight altitude, drone speed, and camera positioning, mainly to account for people on the ground, ensuring safety and accuracy in data collection.
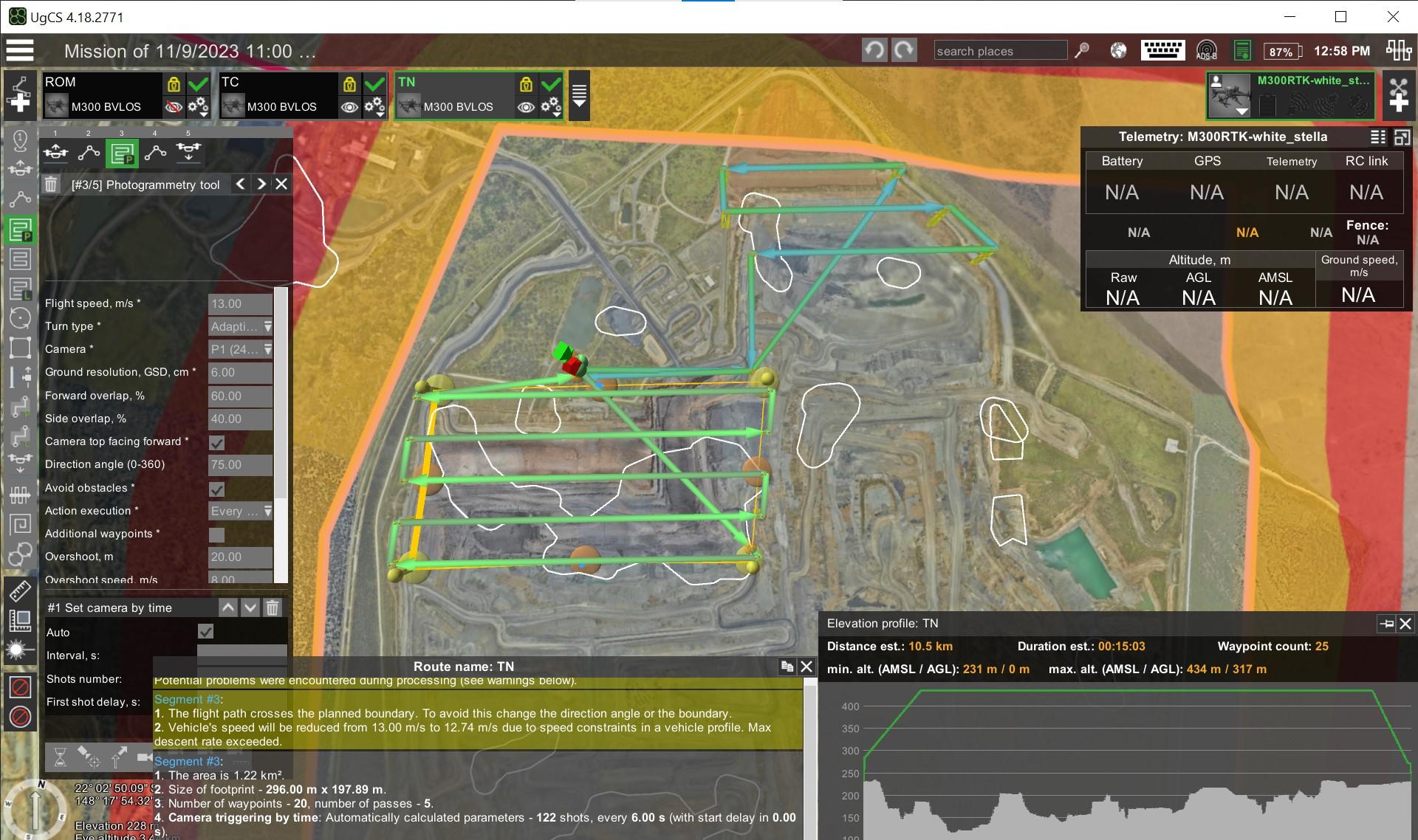
Data Collection
The data collected through these processes are vital for BHP’s operations. Mining surface information and stockpile volumes are processed using in-house machine-learning techniques and photogrammetry software. It allows for faster data acquisition from safer positions at a fraction of the expense of more conventional methods like terrestrial laser scanning.
What drones are commonly used
BHP relies on the DJI M300 and M200/210 drones for their operations. They use the DJI P1 camera for its efficiency over LiDAR in environments with little to no vegetation. The flexibility in camera positioning, whether manual or fixed angles, mainly benefits their operations.
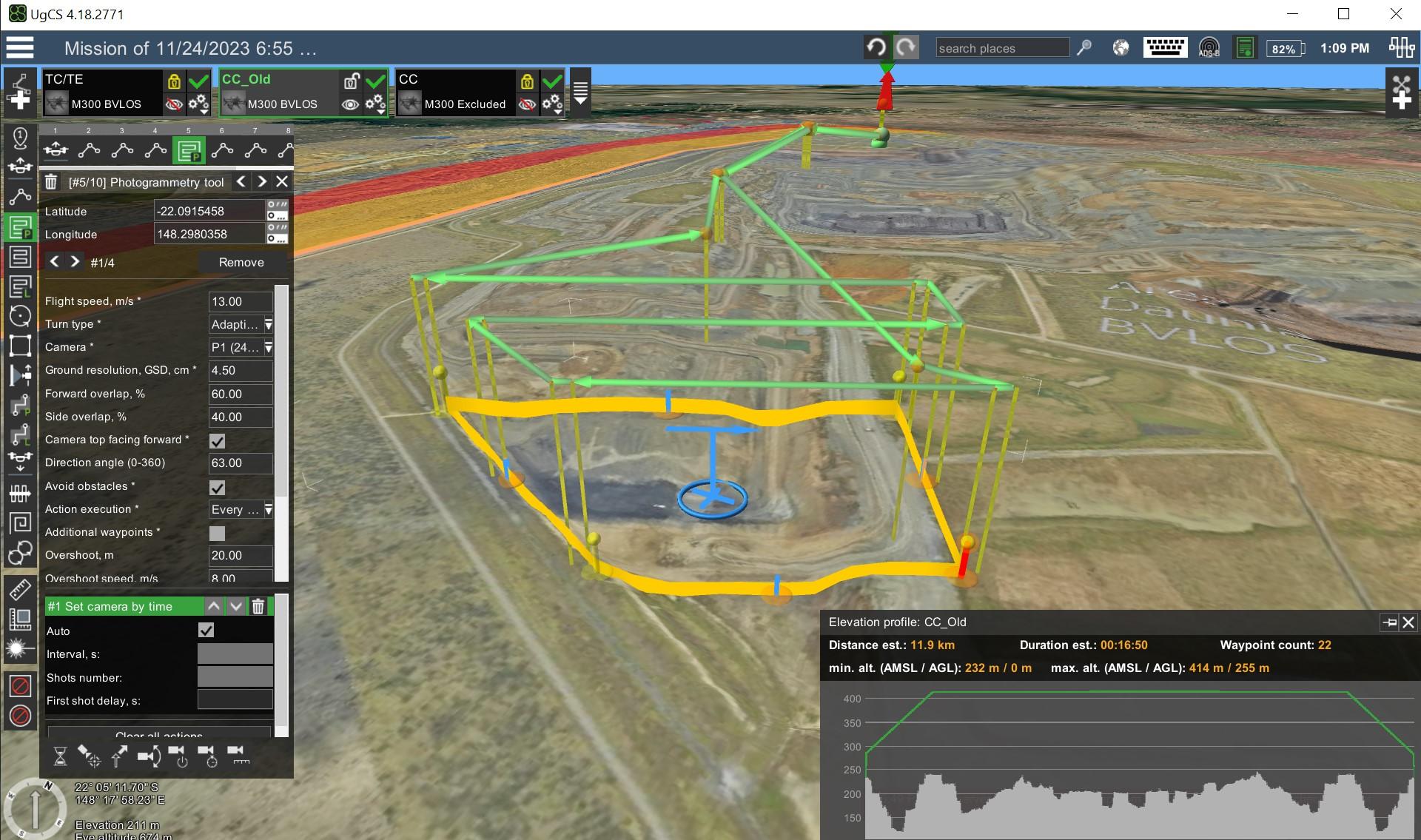
Advantages of UgCS in Mining
UgCS offers significant benefits for mining, saving both time and money. Its automated vertical scanning tool can reduce time spent on tasks from a few hours to several days, depending on the task. By importing digital elevation models and custom maps into its 3D interface, UgCS improves the precision of mission planning and the accuracy of the data models it creates. It also allows for flight operations in remote areas without internet, thanks to its ability to store maps and elevation data. Additionally, UgCS can automatically navigate around obstacles like radio towers or tall buildings, thanks to its no-fly zone feature and smart route planning that avoids obstacles, making it safer and easier to scan hazardous areas.
The Future of Mining with UgCS
“As RPA operations become more complex, we require solutions that display the right information at the right time. UgCS provides us the tools to manage air and ground risks whilst operating a variety of different RPA.” Luke Burton, Chief Remote Pilot
Conclusion
BHP's use of drones, supported by UgCS, shows the critical role of innovative solutions in discovering the full potential of mining operations worldwide.
By tackling problems with land, internet connection, and work efficiency, BHP gets better at what they do and becomes a leading example for others in the industry.