The test was carried out on the 21st of September, 2023, in the SPH Engineering UAV test range in Baloži, Latvia (N 56.8631°, E 24.1119°). Target detection and data processing were done using Seequent Oasis Montaj software. The devices used in this test were MagNIMBUS by SPH Engineering, MagDrone R3 by SENSYS, MagArrow II by Geometrics, and DRONEmag GSMP-35U by GEM Systems.
Data collected by Sergejs Kucenko1. Data processing and report by Matīss Brants1.
1 SPH Engineering SIA, Latvia
Disclaimer
The term "detected" here means that the data interpreter has identified a strong enough signal that warrants further examination or action. Interpretations are subjective and will change depending on the interpreter's experience and knowledge.
Neither SPH Engineering SIA, SENSYS Sensorik & Systemtechnologie GmbH, Geometrics Inc., nor GEM Systems Inc. makes any claims or warranty that detection of the same or similar targets is guaranteed under any conditions other than in the SPH Engineering test range using the same or different hardware, software and workflow.
This report is provided "as is" and is intended to demonstrate the capabilities of the system described herein and provide some guidance for planning utility detection surveys.
Methods
The test setup
Two vehicles, a Volkswagen Touareg 1st Gen and a Ford Mustang 5th Gen, were parked on a 190 m long road adjacent to the drone test range (figure 1). All drone setups were flown along the stretch in different altitudes, from 10 meters to 37 meters above ground level (AGL), in 3-meter increments. The distance between both vehicles was approximately 45 meters. The azimuth of the road is 120°. At the northwestern end of the road were other parked cars and a metal frame building, while the southeastern end leads to a forested area. No metallic objects were sufficiently large along both sides of the road to cause interference at the tested altitudes. More than 20 meters at the ends of the flight path were used as run-off to decrease the influence of speed changes and turns.
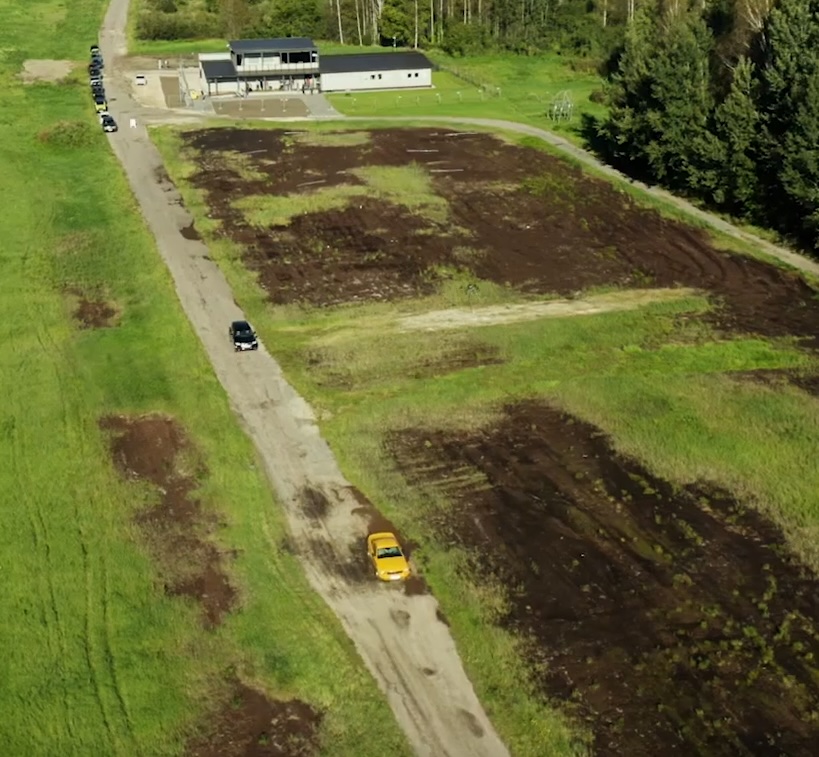
Magnetometers
All magnetometers were attached to a DJI Matrice 300 RTK UAV, which utilized GNSS (Global Navigation Satellite System) with RTK (Real Time Kinematics) for precise positioning. For geotagging, it was used a different approach for different magnetometers:
- MagNIMBUS: data logging is on SkyHub onboard computer using coordinates stream from the drone’s GNSS receiver, which was in RTK mode during the tests.
- MagDrone R3: that magnetometer has an internal data recorder, but the coordinates stream was supplied from the drone’s GNSS receiver through the SkyHub onboard computer.
- MagArrow Mk2: it has an internal data logger and internal RTK GNSS receiver, but during the tests, it was in non-RTK mode. After the flight coordinates in the data were replaced with precise coordinates from the flight log, which was recorded by SkyHub (the drone was in RTK mode).
- DRONEmag GSMP-35U: it has an internal data recorder, and a separate GNSS receiver was connected directly to the recorder. That GNSS receiver was in non-RTK mode, and coordinates in logged data were refined using flight track recorded by SkyHub.
MagNIMBUS
The SPH Engineering manufactured MagNIMBUS system (figure 2) utilizes a QuSpin Total-Field Magnetometer placed at the end of a collapsible "arm" under the UAV, which protects the system from damage in case of a collision with unexpected obstacles and permits extremely low flights with relative safety. The QuSpin sensor records total magnetic intensity at a rate of 500 Hz, which allows it to filter out any magnetic noise picked up from electrical parts of the UAV and nearby alternating electromagnetic sources like power lines. The setup was flown at a constant speed of 5 m/s.
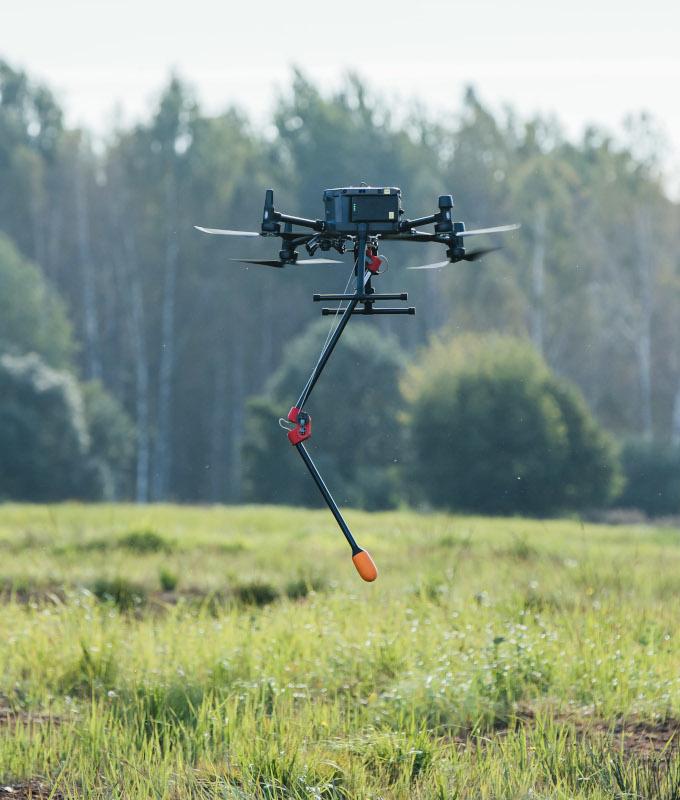
MagDrone R3
The MagDrone R3 by SENSYS GmbH is a magnetometer system (figure 3) with two 3-axis fluxgate vectorial sensors built into the ends of a one-meter-long tube. This dual-sensor setup reduces flight time by at least 50% compared to single-sensor setups. The device is attached directly to the legs of the UAV, thus providing stable and relatively predictable sensor movement while also placing the magnetometers closer to the magnetic interference of the motors of the UAV. Both sensors record the magnetic field in all three axis at a sampling rate of 250 Hz to allow the removal of the alternating noise of UAV's motors and other sources like power lines. The setup was flown at a constant speed of 5 m/s.
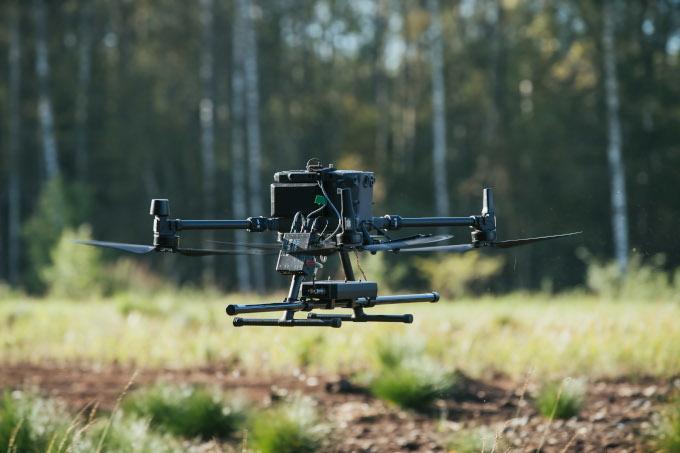
MagArrow II
The Geometrics MagArrow II magnetometer (figure 4) utilizes a wire-suspended setup in an aerodynamic enclosure to place the total field magnetometer sensor as far away from the interference of the UAV as possible. Even with such a placement, the very high sampling rate of 1000 Hz allows for filtering any remaining alternating magnetic noise caused by the UAV or any other sources, such as power lines. The suspended setup increases the movement of the magnetometer encasement, causing magnetic field reading changes; thus, a heading calibration flight is highly recommended. For this test, the MagArrow II magnetometer was suspended in a 3-meter-long cable system, and the flight was done at a constant UAV speed of 4 m/s.
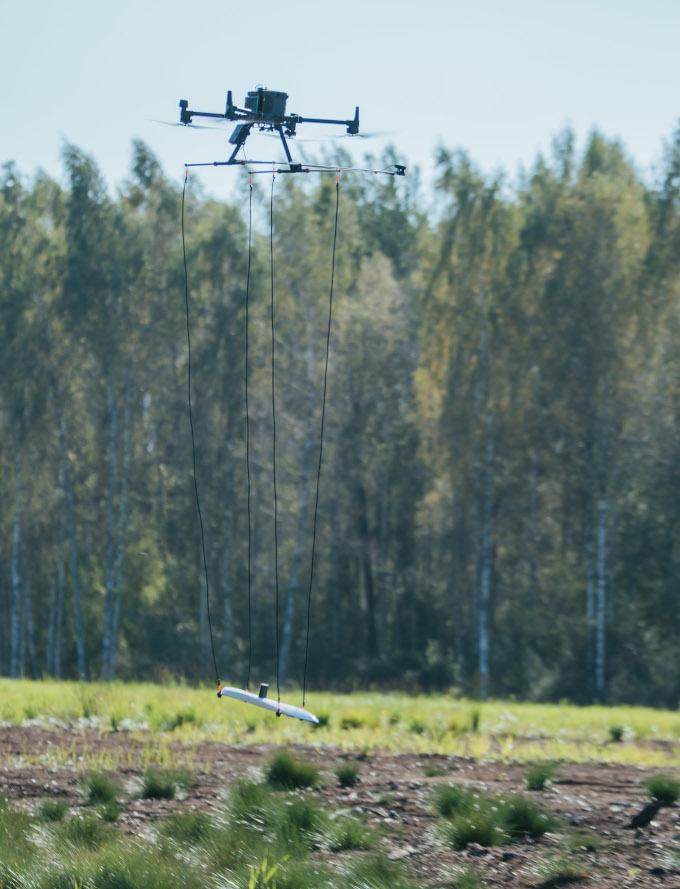
DRONEmag GSMP-35U
The GEM Systems DRONEmag GSMP-35U is a total-field magnetometer system (figure 5) suspended in a 3-5 m cable from the UAV. This setup provides maximum distance from the magnetic interference of the UAV's motors. Such a setup allows for a much lower sampling rate of a maximum of 20 Hz than the manufacturers' sensors. A low sampling rate also provides easier and faster data processing. The setup was suspended in a 5-meter-long cable and flown at a constant UAV speed of 4 m/s.
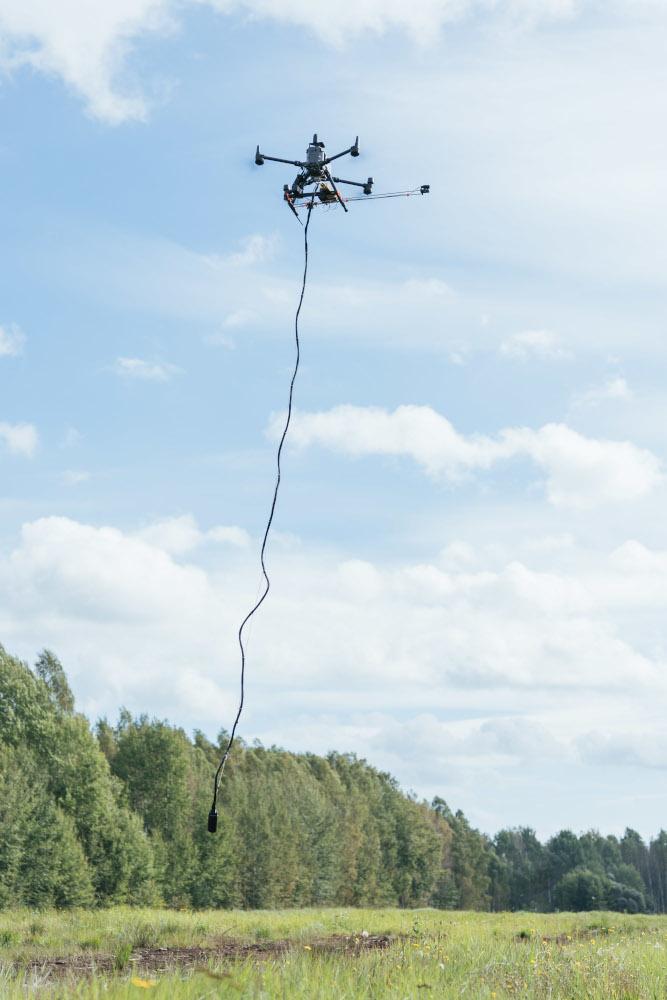
Data processing
Magnetic data processing was done similarly for all systems except for specific data format conversions for MagDRONE R3 and MagArrow II systems, which required proprietary software. The general workflow is outlined in Figure 6, with a detailed step-by-step account for all setups in the Appendix. The main software used was Geosoft Oasis Montaj Standard Edition v.2023.1. utilizing only the base module features and well-documented processing methods. All the steps may be repeated with similar results using closed and open-source software. The processed data was visualized as a 1D residual magnetic anomaly line at different heights using the Python module Pandas.

Results
All sensors detected separate magnetic field signals of both vehicles at a height of up to 25 m AGL. It must be noted that at the maximum altitude of 37 meters, the magnetic field from both cars is at the threshold of being physically inseparable.
The MagNIMBUS sensor data (figure 7) clearly shows two separate magnetic signals up to 28 meters above ground level (AGL). In contrast, the signal at higher altitudes seems somewhat ambiguous due to noise (most likely caused by swaying in wind). But even up to 37 m AGL there is a visible rise in the magnetic signal near the vehicle positions, although this might just be a coincidental artifact caused by removing regional magnetic trend.
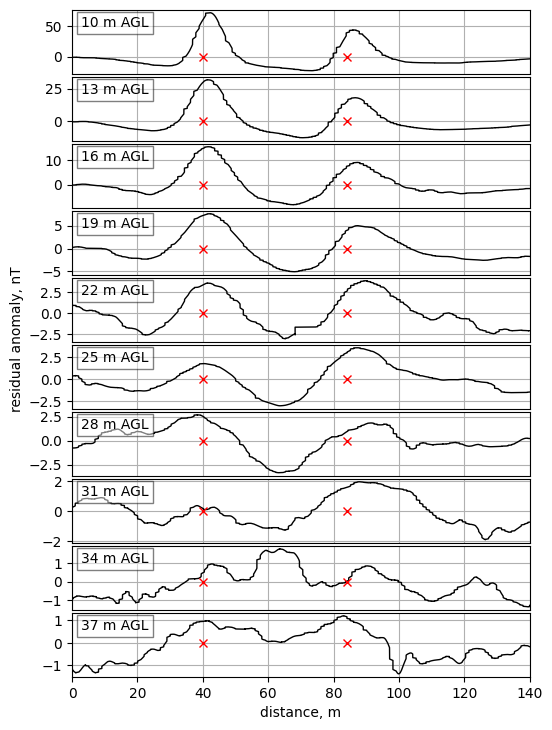
The MagDrone R3 sensor (figure 8) performed similarly up to a height of 28 m AGL, where both vehicle signals can still be identified. Still, at higher altitudes, the noise is too intense to discern any changes caused by vehicles. This is likely due to the higher noise floor of the MagDrone R3 sensor, but the wind effect also needs to be considered. The low peak from the second vehicle at 10 m AGL was caused by mistakenly routing the drone off the course.
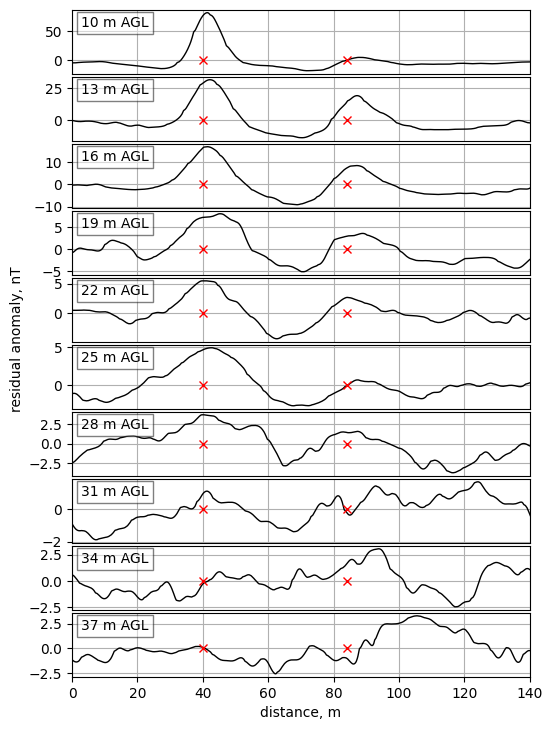
The MagArrow II data (figure 9) show two clear peaks up to 25 m AGL. In contrast, at 28 m AGL, there seem to be some distortions in the signal (likely due to the sensor swaying in the wind), but it would most likely still be considered a positive detection. Two signal peaks are somewhat visible at 31 m AGL and, to a lesser extent, at 34 m AGL. At 37 m AGL, there is no visible anomaly in the vehicles.
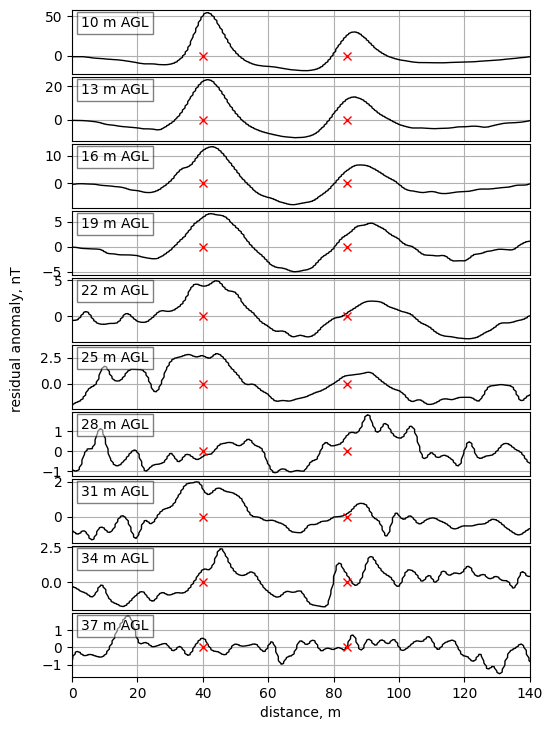
The GSMP-35U shows the best results (Figure 10) by clearly detecting both vehicles at a height of up to 34 m AGL. Possibly, it is even 37 m AGL, although this might be due to the removal of the regional trend, as with the MagNIMBUS sensor. The results of the GSMP-35U, most likely, are due to the very low noise floor of the sensor.
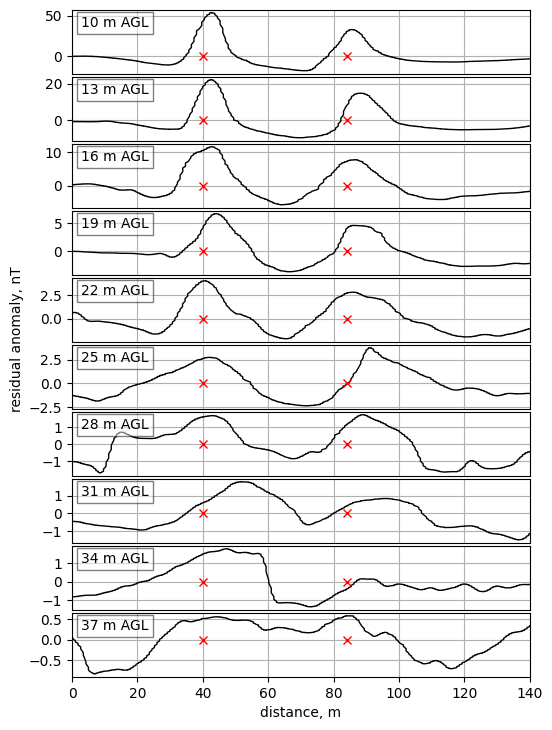
Conclusions
- The magnetic signals from two test vehicles were detected by all sensors at a height of up to 25 meters above ground level (AGL), after which the results started to vary.
- The GSMP-35U performed the best by still detecting a notable signal at a height of 34 m AGL.
- The MagArrow II and MagNIMBUS might have also detected the vehicles at the highest altitudes, but the results are ambiguous.
- The MagDrone R3 didn’t show any clear signal above 28 m AGL, likely due to the higher noise floor caused by the sensor mounted near drone motors.
- When doing a magnetic survey where the magnetic signal is expected to be just above the sensor noise floor, moving any nearby vehicles at least 40 meters from the survey area is advised.
Appendix - data processing steps
MagNIMBUS
- Split data into lines by altitude;
- Applied Low-pass filter 500 fiducials (5 meters);
- Applied Lag correction of -150 fiducials;
- Removed 1st order polynomial trend and created a residual;
- Removed 2nd order polynomial trend and created a residual (used in data interpretation).
MagDRONE R3
Using MagDrone DataTool:
- Divided into tracks.
- No filters or downsampling.
- Loaded GNSS RTK data.
- Exported to .asc file.
Using Oasis Montaj:
- Split data into lines by sensor and altitude;
- Applied Low-pass filter 250 fiducials (5 meters);
- No Lag correction was needed;
- Removed 1st order polynomial trend and created a residual;
- Removed 2nd order polynomial trend and created a residual (used in data interpretation).
MagArrow II
Using Geometrics Survey Manager:
- Data converted from MagArrow .magdata to .csv data format.
Using Oasis Montaj:
- Split data into lines by altitude;
- Applied Low-pass filter 1250 fiducials (5 meters);
- Applied Lag correction of +150 fiducials;
- Removed 1st order polynomial trend and created a residual;
- Removed 2nd order polynomial trend and created a residual (used in data interpretation).
GSMP-35U
Using Oasis Montaj:
- Split data into lines by altitude;
- Applied Low-pass filter 25 fiducials (5 meters);
- Applied Lag correction of +18 fiducials;
- Removed 1st order polynomial trend and created a residual;
- Removed 2nd order polynomial trend and created a residual (used in data interpretation).